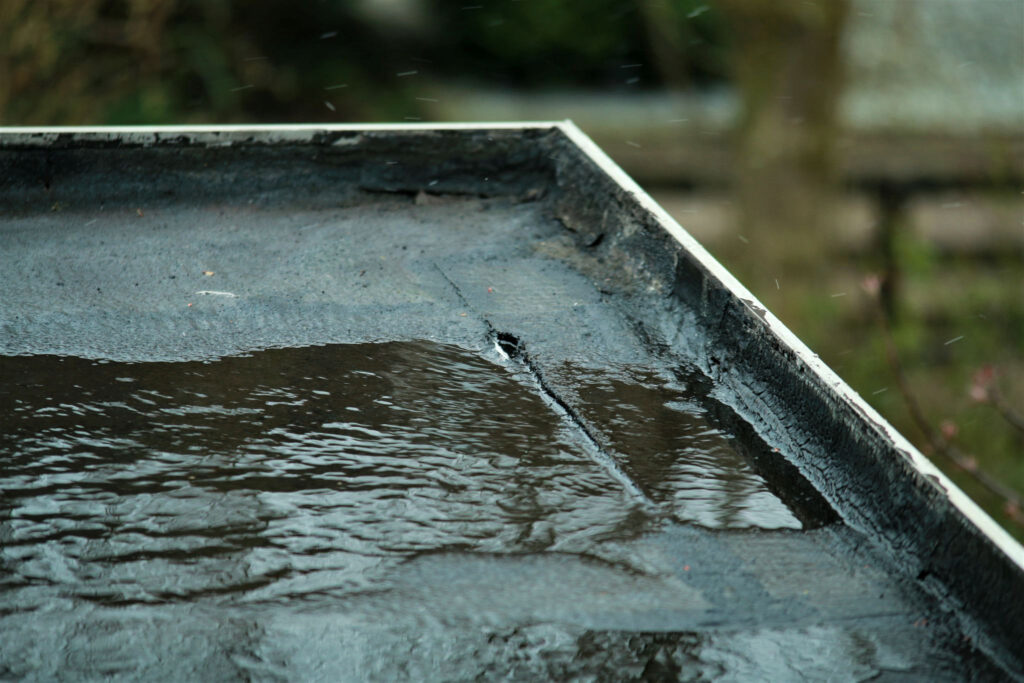
The National Fire Protection Association (NFPA), The Joint Commission, the Centers for Medicare and Medicaid Services, and many states, municipalities, and building code accrediting bodies are cracking down on the deferred maintenance that’s increasing risk to staff and patrons at aging healthcare facilities. More specifically, it’s not that they’re cracking down on the maintenance so much as they’re looking at failing building fire, smoke, lighting, doors, generators, and sprinkler systems that are showing their age.
Aging buildings from the 1950s and 1960s can frequently handle significant voltage. All the old freezers and appliances of that era were nowhere near as energy efficient as appliances are today, so buildings can often handle several hundred amps. But because we now require power for many more appliances, tools, and equipment, including high-energy medical hardware, the energy efficiency savings have been surpassed by sheer electrical volume needs.
The NFPA’s Life Safety Code, the Joint Commission, and CMS are increasingly finding
- Fire doors that don’t close properly or fully
- Penetrated smoke barriers
- Overloaded circuits, and
- Emergency generators that fail tests because of dying batteries or a lack of juice to power the critical systems needed.
- Plus hallways and stairwells are increasingly crowded, sometimes with patient beds, and are thus obstructed.
Deferred maintenance costing commercial and industrial operations
It’s not just healthcare facilities and hospitals facing issues. The NFPA and American Society of Heating, Refrigerating and Air-Conditioning Engineers (ASHRAE) both maintain accreditation standards used by engineering firms around the world. Engineers increasingly find
- Leaking doors and windows that lead to mold infestations
- Worn HVAC units that can’t keep up with the public demand for air quality and ventilation
- Warped floors, past sub-par retrofits, and old electrical panels that aren’t ARC-fault protected round out the list.
All these engineering and mechanical problems are just as harmful in a school, apartment building, factory, commercial freezer, or warehouse as they are in a hospital or medical facility.
Costs are high as supply chain and supply and demand impact labor
No good cost estimate exists of how much deferred maintenance is piling up across US healthcare facilities. Federal medical facilities have a backlog that is as high as $20 billion. It’s not hard to see why.
- A generator replacement can cost between $ 100,000 and $ 500,000.
- A fire alarm panel and components can be $50,000-$200,000, depending on the building.
- And a sprinkler system at a mid-size facility can cost up to a million dollars.
As even average homeowners can attest, mold remediation, electrical repairs, plumbing replacement, and new roofs are also expensive.
There are four primary factors that contribute to these projects being expensive and deferred:
- Skilled labor to fix building issues is scarce, and supply and demand is driving up costs.
- Many facilities increasingly follow a “run to fail” culture, under the assumption that running a system until it fails is ultimately better business and environmental sense than replacing it. But as anyone with a 50-year-old deep freezer in their basement knows, “It might run, and it works, but it’s not efficient and is a little bit risky.”
- U.S. building codes have high standards that ultimately drive up costs, like earthquake protection in California or hurricane-resistant buildings along the Gulf or East coasts.
- For private hospitals striving to maintain profits for shareholders, the cost of replacement is “another expense.” In fact, many large hospitals with the capacity to carry high debt service find it cheaper to build new hospitals since federal reimbursement rates are higher for “new construction” facilities than for existing facilities.
In the short term, this lack of maintenance seems almost prudent. But the long-term costs double, triple, or quadruple the overall costs. A leaky roof that keeps getting patched has leaks you don’t see. Those leaks form mold, and suddenly a roof replacement also includes new supports, mold remediation, and other hidden costs. All of which will ultimately show up on an inspection report and can result in a loss of income from closed or cited facilities.
What you can do to get a handle on deferred maintenance
There are practical steps facility managers can take, and it starts with a complete inventory and honest assessment. When VPC conducts on-site Safety Checks, we notice the problems that fire, Joint Commission, and other inspectors are going to notice, too. But when we notice it doesn’t result in a citation or risk of a heavy fine.
- Create a Facility Condition Index to account for all your building’s mechanical, electrical, plumbing, and technological systems.
- Include the roof, flooring, windows, doors, fire suppression, energy generators, and building envelope.
- Identify their age, their expected lifespan, and when if any repairs or replacements have been partially completed.
- As capital improvement projects come along, advocate for safety projects to be bundled in. They’re part of a capital campaign, too.
- Budget appropriately for major projects that are 3, 5, 10, or even 25 years down the line.
- Account for “the cost of doing nothing”. Just like the “cost of doing business”, doing nothing can be more costly.
- Consider a third party assessment. VPC consults can help you spot problems like Joint Commission or fire inspectors would, including items you might not even be aware of, helping save you more money from fines and fees.